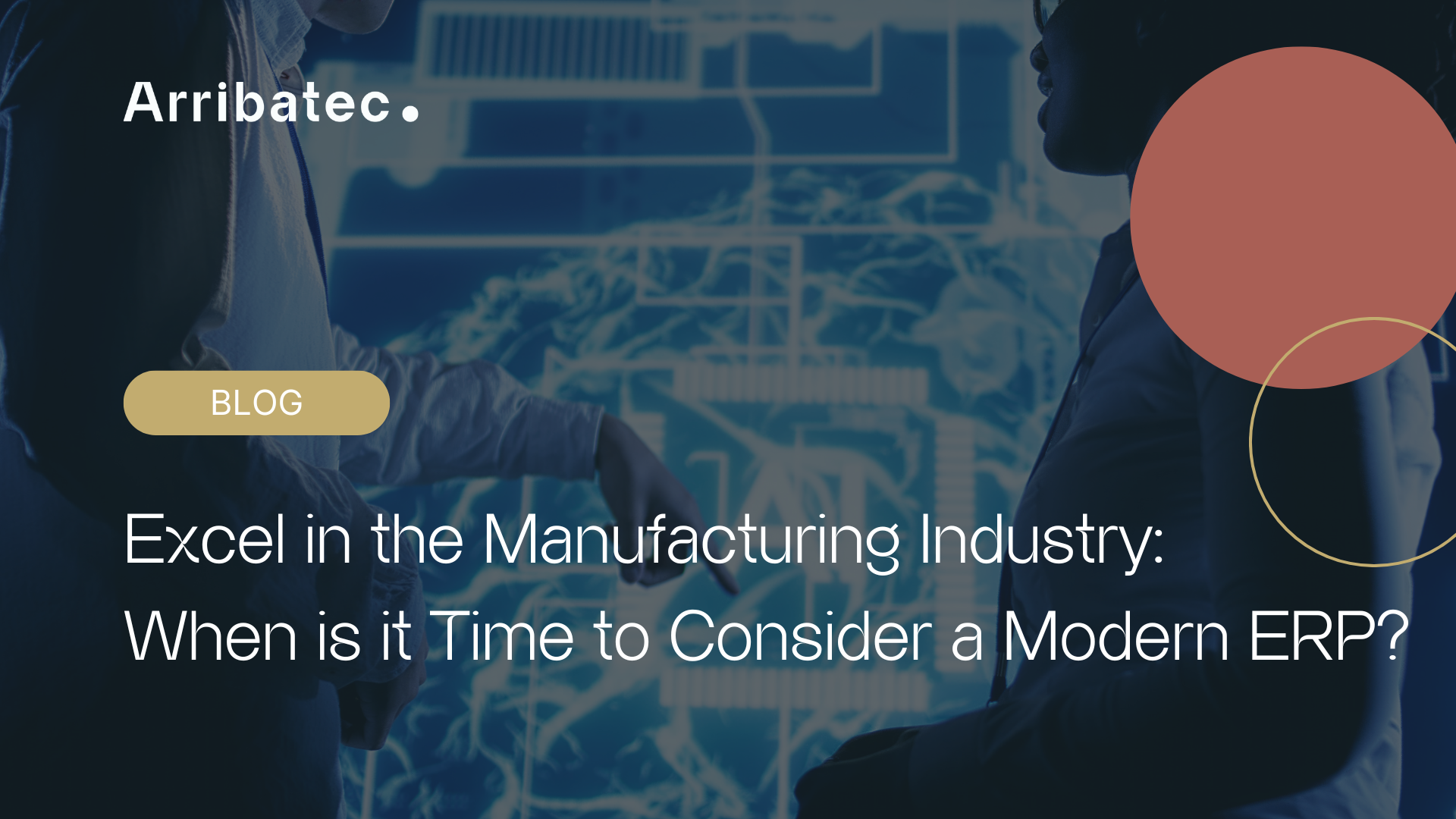
France and Norway are different but complementary in their approaches to why mid-sized businesses are reassessing ERP, and why SAP is winning.
Excel in the Manufacturing Industry: When is it Time to Consider a Modern ERP?
Many manufacturing companies I speak with rely too heavily on Excel – for everything from sales and planning to production and finance. It has been a flexible solution for many, but more and more are starting to feel the limits of what spreadsheets can handle. As complexity increases and the need for real-time data, traceability, and control grows, the question arises: When is it time to consider an ERP system?
By: Jørgen Borvik
Everyone Has Some Kind of Excel Sheet
Everyone loves Excel. It’s versatile, flexible, and relatively easy to use. That’s why you’ll find numerous Excel sheets in every part of a business you examine: sales, planning, purchasing, production, finance, and quality. While spreadsheets have their limitations, people quickly get used to them and create “workarounds” that function reasonably well. But beneath the surface lie major challenges – and even greater opportunities. Once the honeymoon phase is over and reality sets in, many develop a love-hate relationship with Excel.
When Excel Becomes a Bottleneck
As the business grows, Excel can quickly become a bottleneck and a brake on growth if it’s used for tasks it simply wasn’t designed to handle. Here are at least five reasons why:
Manual errors and financial loss: Where there are spreadsheets with formulas, there is room for mistakes – from inventory inaccuracies and incorrect calculations to customer communication breakdowns and lost sales opportunities.
Time-consuming and inefficient: Employees spend too much time updating and checking spreadsheets (and dealing with uncertainty around outdated versions) instead of creating value.
Lack of real-time data: Excel only shows historical data. You don’t get real-time insights into inventory, deliveries, production, or finance. This makes fast, informed decision-making nearly impossible.
Poor collaboration and silo mentality: When multiple departments work in the same sheet, it often leads to duplicated work, misunderstandings, and slow information flow. The new column you added yesterday may suddenly be gone. Then you need to check change logs, who edited what, and why. Little value in that.
Difficult to scale: As the business grows, Excel sheets swell in complexity and size. The more people who work in them, the greater the risk of manual errors. Eventually, you become overly dependent on a single Excel guru who becomes irreplaceable. This increases the company’s vulnerability – and it’s completely avoidable.
Recurring Challenges in Manufacturing Companies
As an advisor for nearly 15 years, I’ve sat down with companies looking to streamline their business processes. While these companies span all industries, recently the focus has been primarily on manufacturing companies – together with skilled professionals on our delivery team. Whether clients are located in a fjord in Western Norway, on the northern coast, or by a motorway in the East, they tend to share similar challenges when it comes to optimising ERP processes. Let’s look at how these challenges present themselves across different parts of the value chain, for companies using Excel or other manual or underpowered solutions.
Data Flow from Design to Sales
For those designing products, or receiving technical drawings from clients via a CAD/PDM system, the flow of data and version changes often requires unnecessary manual entries into ERP. In many cases, proper integration is lacking. This makes maintaining BOM structures and creating accurate sales quotations time- and resource-intensive, which ultimately impacts production predictability and customer experience.
Estimates vs Actuals
A cost estimate is a projection; actual costing is the result. Many companies may have an overview of total revenue and cost of goods sold on an order, but struggle with detailed tracking when comparing estimates to actuals. Where are margins lost – sales price, cost price, time and material usage, operator efficiency, or manual documentation? Being able to track cost development throughout the delivery is valuable. Without that insight, it’s hard to optimise sales and production.
Material Requirements, Purchasing and Inventory
Without control of material needs, you’re likely to either have an overstocked and expensive warehouse or fail to deliver to customers on time. This is especially tricky for manufacturers, as material demand arises from several sources (sales, production, minimum stock levels, forecasts, etc.) with frequent changes. Without system support, it becomes difficult to manage customer dialogue and to adjust and improve these processes.
Production Planning
To know if you can deliver on time, you need visibility of capacity, lead times, orders, material needs and priorities. That requires a full overview of both the BOM and routing – what needs to be done, in what order, and on which machines/resources, based on capacity. Many companies lack data flow and updates across systems, making accurate planning difficult. IoT and real-time data are available to many, but rarely used to their full potential.
Production
Operators must deliver on time, with the correct documentation (e.g. MRB requirements from customers) and full traceability. Changes during production in consumption or resources must be captured – but this rarely happens systematically, making continuous improvement difficult.
Documentation Requirements and Traceability
Manufacturers often face strict requirements for quality and traceability across the entire value chain, from raw materials to finished product. Still, measurement data, tolerances, and deviations are often recorded in separate Excel sheets or on paper, making post-delivery documentation a major challenge. Traceability back to batch/serial/heat numbers and goods receipt should be documented at a much more detailed level in the ERP system. That would give better control, higher quality, and reduced risk during audits or in the event of customer complaints.
Finance and Reporting
When key figures are pulled from various systems, spreadsheets, and manual routines, reporting becomes time-consuming and difficult to quality-assure. Without a comprehensive overview, it’s harder to monitor margins, value creation, and alignment between purchase orders, goods receipt, and invoicing.
Benefits of Moving from Excel to a Future-Proof ERP System
Today, there are professional ERP systems specifically designed for manufacturing companies, built on the experiences of businesses like yours. RamBase ERP is one such system. The advantages of moving from spreadsheets to this kind of ERP solution are many, but here are some of the most important:
You get real-time data across the entire organisation – from sales to production and finance – all in one platform. No more manual entry, and many processes from order to payment can be automated. Every company wants to “do more with the resources they have” (read: be more efficient).
You gain control. Traceability. Insight. And you standardise processes so that knowledge stays in the business, not with individuals (people come and go – they always will).
Security is higher, thanks to the cloud provider’s investments in encryption, monitoring and backup.
The system grows with you. It evolves continuously based on customer needs and market changes. And yes, that includes support for increased use of artificial intelligence (AI). This means you’re future-proof – no more falling behind the times.
In Summary
Excel is still the glue holding many manufacturing companies together. But for many, that glue is starting to crack at the seams. A modern ERP system can provide better oversight, greater predictability, and less manual work. That doesn’t mean one solution fits all.
What’s most important is being honest with yourself: Are your current tools preventing you from working the way you actually want to? If so, it might be time to raise your sights and take the step into a professional ERP system made for industry.
As for timing? It’s never perfect – but the cost of doing nothing and continuing as before is very real. You just don’t know how big it truly is.
Perhaps because you’re spending too much time in Excel.